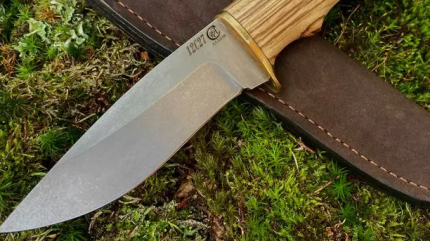
In 2024, sustainability is a regulatory requirement. If global economies are to reach net-zero goals by 2050, businesses involved in carbon-intensive manufacturing must rapidly shrink their climate footprint. The production of steel, largely made in coal-fired blast furnaces, accounts for about 7% or 8% of the world’s greenhouse gas emissions.
Steel is central to our everyday lives, used to make everything from ships to buildings to knives, and so national decarbonisation plans must include manufacturers cutting steel-related emissions. For knife makers, sustainability is now as important as performance factors, like edge retention, resistance to corrosion, and hardness, according to Jonas Nilsson, business development project manager at Alleima, which has produced martensitic stainless chromium knife steels for more than 100 years.
“Our customers and their customers, the end-users, are asking about it and changing their buying behaviour to be more sustainable.”
Green credentials: what to look out for
At the same time there is growing awareness around greenwashing – where companies enhance sustainability claims for marketing purposes – and scepticism around ESG-oriented certifications. The US, UK and the EU have recently been reviewing their green claims guides and legal frameworks. Businesses should think twice before making unsubstantiated claims or be at risk of legal action.
Nilsson says that energy efficiency, recycling and reducing waste, and complete transparency and due diligence in the supply chain is the only way to make sure that sustainable steel practices have been followed and enable knife manufacturers to claim green credentials.
This is how Alleima is meeting that demand.
Most of the energy required in steel production is used during melting and heat-treating operations. Some of these furnaces are electrically heated with fossil free electricity, while others require gas. Historically, petroleum gas (LPG) was the main fuel, but in 2016 Alleima switched to a natural gas that has 10% to 15% lower CO2 emission, and since 2020 some of this natural gas has been replaced by biogas made from food waste and other biological sources. During 2024 Alleima aims to use green hydrogen as the energy source to cut the strands in the continuous casting process.
Energy efficiency is also important in other stages of production, even when they are less energy intensive. Diesel-powered vehicles for internal transport on the site in Sandviken are fuelled by HVO, a biodiesel made from renewable sources that removes 2000 tonnes per year of CO2.
In 2002, Alleima, certified according to the environmental management system ISO 14001 and in 2006 the energy management system ISO 50001.
Committed to cutting Scope 1 and 2 CO2 emissions in half, Alleima has said it will be providing 83% recycled steel in finished products and reaching waste circularity of 76% by 2030.
Building a sustainable supply chain
Sustainable supplier management is a prioritised area for Alleima, as it is essential to only do business with suppliers that share a commitment to environmental, social, and governance (ESG). Alleima has a six-step supplier due diligence process built upon OECD due diligence guidance for responsible business conduct, which is a general process to identify, assess, mitigate, and remedy adverse impact in the supply chain.
Complying with Alleima’s Supplier Code of Conduct is a prerequisite for doing business with Alleima, and a basis for ensuring a sustainable supply chain. All suppliers (in scope) must be risk screened, with regards to sustainability, using a credible ratings tool like EcoVadis.
EcoVadis helps Alleima to monitor supplier compliance and provides a scorecard of supplier performance and an overview of their improvement areas. Alleima also carries out more general evaluations, going directly to the source to assess CO2 emissions from each raw material supplier.
“The biggest supply challenges come in mining of virgin materials. Alleima forms long-term relationships directly with the mines and producers, not with intermediaries, and only does business with the companies that have the smallest negative effects on the environment,” says Nilsson.
Recycled steel is premium steel
Sustainability and recycling are not fad trends for Alleima, which has been producing recycled knife steel since 1921. One hundred years later, the share of recycled material in Alleima’s knife steel (Alleima 12C27) is at 81% according to its internal definition (amount of recycled material added to each heat divided by the weight of total material added).
This high rate of recycled material does not compromise on the quality of the knife steel, as Alleima is stringent in controlling recycling processes. By controlling the allowed maximum levels for certain critical elements in the recycled material, the quality of the finished recycled product achieves the same properties as if the material would have been produced from virgin raw materials.
As well as diligently controlled internal recycling, Alleima buys a major part of the material needed for production from the recycled steel market, where the composition is well understood. The company uses calculation models to guide its use of recycled material when developing the chemical composition of a new melt, usually adding between 5% and-25% of virgin alloy elements to adjust the final composition and always avoiding conflict minerals such as cobalt and tungsten in knife steels.
When developing new knife alloys, the focus is on improving critical knife properties such as corrosion resistance, edge holding capability, toughness and re-grindability so that the final knife can have a long life. After the end of the life cycle for the knife, it can be remelted to make new steel products.
We believe we are setting new standards for the knife steel industry,” Nilsson says. “By integrating energy efficiency, recycling, and transparent supply chain practices, Alleima is not only responding to the growing demand for sustainable products but is also leading by example in the pursuit of environmental responsibility.
“Our commitment to using recycled materials, combined with rigorous quality control, ensures that sustainability never comes at the expense of performance.”
Explore Alleima’s capabilities in developing sustainable precision strip steel in the whitepaper below.